The need for cost-effective and reliable testing solutions has increased the demand for non-destructive testing technology (NDT) and quality control management systems.
With the implementation of intelligent non-destructive testing technology & quality control management, companies have been able to bring about significant cost savings and improve productivity by conforming to strict guidelines set forth by international standards. Read on for all you need to know about non-destructive testing technology (NDT) and quality control management.
What is Non-Destructive Testing Technology and Quality Control Management?
Non-destructive testing (NDT) is a form of testing that involves using methods and techniques that don’t permanently damage or destroy the product being tested. Often called non-disintegration testing, this methodology focuses on obtaining data that will help determine the integrity of a product or component and allows the testing of various products with minimal disruption to the working process.
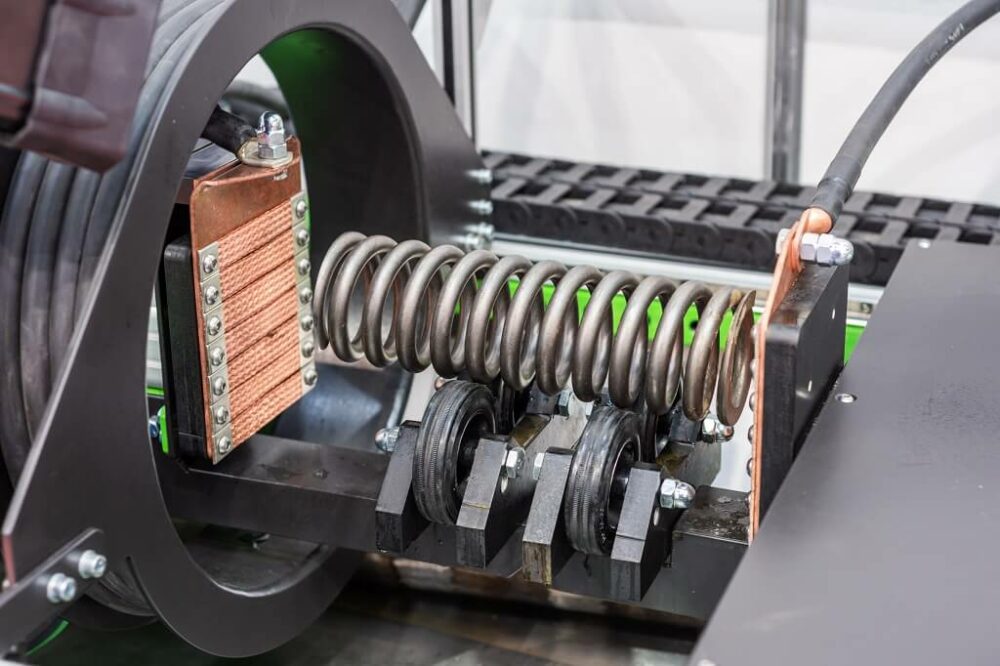
The array of inspection tools used to perform NDT includes automated ultrasonic testing (AUT), visual testing (VT), liquid penetrant inspection (PT), and magnetic particle testing (MT).
On the other hand, quality control is the process of testing, inspecting, and measuring the final outputs of a product to verify if it conforms to all the accepted standards stated during quality planning.
Quality control management aims to ensure a product’s quality is maintained or improved before being passed on to the consumer. Quality control detects and corrects defects in an already finished product. It aims at standardizing both production and reaction effects to quality issues.

The importance of non-destructive testing technology as a quality control tool in the industry domain can’t be overemphasized. Nowadays, many industries, including people looking for a career in aviation, manufacturing, and construction use these to evaluate products’ manufacturing processes and maintain a required uniform quality standard. This is to ensure that safe and reliable products are delivered to the public.
These testing and analytical methods are pertinent to many companies’ everyday functions. It ensures that all activities involved in a product are done according to the approved specifications and procedures.
Non-destructive technology plays a significant role in quality control management when carrying out analytical procedures for the safety and reliability of manufactured products. Here are some of the ways NDT affects and helps quality control management:
1. Balance Quality Control Management.
The value of stringent quality control & quality assurance is well known within most industries. However, companies fail to live up to these expectations in many cases, thereby placing themselves at undue risk. As a result of quality control failures, many products are rejected by consumers when the marketer fails to meet expectations.
Furthermore, as companies struggle to meet consumer demands, they begin to cut costs by implementing cost-cutting measures and employee layoffs. This often leads to a significant reduction in quality and efficiency – two key components to achieving success within a company. By using intelligent non-destructive testing techniques, a company can avoid the problems mentioned above and maintain high customer satisfaction levels.
2. Manufacturing Failure Process.
Most defects in products usually occur during the manufacturing process. It’s important to have materials go through non-destructive technology inspection processes once production starts to detect concerns before reaching the end product stage.
Components in products that fail to meet the quality standard can be expensive to replace or repair. It can lead to a business closing and will also cause adverse effects for consumers. What’s worse, some manufacturers may decide to ignore this issue as it may affect their productivity level.
Non-destructive technology can prevent this by identifying such faulty components before they reach the final production stage. Thus, with the use of non-destructive technology, quality control is assured for consumers.
3. Approved Quality Protocol.
Non-destructive technology is one of the many test standards employed in conducting quality control tests for a product. Assessing a product or substance through non-destructive technology is a means of ascertaining that the product has been tested and evaluated following the guidelines and regulations provided by quality control management.
Non-destructive technology points out areas of concern before failure and identifies the weaknesses and errors to rectify them and prevent a recurrence.
4. Guarantees Comprehensive Testing.
The main purpose of doing quality control is to ensure positive clarifications of the features of a product. Non-destructive technology makes this easier by doing thorough, comprehensive tests for products.
The fact that NDT is performed to determine the structure, composition, and properties in a product without missing any part of it guarantees that all components of the material will be tested. Both the internal and surface material of products can be tested for quality purposes. This will ensure that the quality of the products produced complies with the required quality standards.
5. Product Reliability.
Advanced and more comprehensive testing guarantees great products. Non-destructive technology assures the reliability of the structures and components of products by inspecting the condition of all the elements in and out. The materials are tested in a way that doesn’t affect the product.
This makes it very useful for determining the safety and integrity of products that are being used or will be used in the future. Besides, industries that use non-destructive technology to evaluate their products’ components can confidently say their products are reliable. Non-destructive technology provides a means of performing quality control tests to ensure products are reliable and safe for consumers.
6. Identifying Defects In Production Material.
Non-destructive technology is an effective way of checking the quality of a product’s manufacturing processes. Because it can be applied at any stage of manufacturing products, this helps quality control technicians to easily detect any impairment in the material and identify or replace it before it gets to the final stage.
Non-destructive technology can be performed before a product is finished and as well as after the production. The problems are identified through the use of non-destructive technology that doesn’t compromise quality or functionality.
7. Convenient Quality Control Process.
The advancements in non-destructive technology have significantly improved the test’s efficiency and accuracy for quality in products. Even products that can’t be tested for quality purposes because they’re being produced in remote areas and environments that aren’t accessible for quality control officials can now be readily assessed using advanced non-destructive technology remotely.
Most of this equipment can be set up quickly to conduct an inspection, especially the portable and the mobile compatible ones. The advancement of NDT reflects on the processes involved in running a product’s quality control test. This improvement has also helped manufacturers to check the quality of their products conveniently.
Conclusion.
Non-destructive testing technology is a vital aspect of quality control management. The application of NDT has led to an increase in product life span and profitability for manufacturers. It has also improved efficiency, reduced cost, and quality control. These benefits have helped countless organizations to leverage non-destructive technology to gain a competitive advantage within their industry. Given the positive benefits of non-destructive technology, this innovative technique is expected to grow in importance and significance in years to come.